Risk Management Framework
The management of risk is defined by a framework of control measures which prioritise the highest forms of protection down to the lowest. This risk management framework, or hierarchy as it is also known, breaks various risk control methods into three levels ranging from most effective to the least reliable. Under OHS laws and regulations, duty holders are required to work through this framework when conducing risk management in construction.
This is a fundamental part of knowing how to perform a risk assessment.
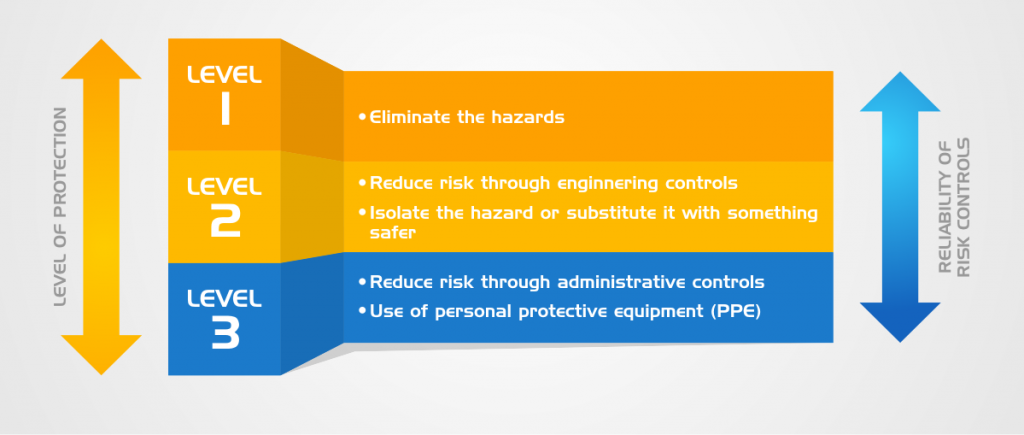
Level 1 of risk management strategies
The best way to reduce risk in a workplace is by eliminating all hazards completely. For instance, if there is a risk of falling from heights then the best risk management strategy would be to work from the ground level instead. The same applies for hazards like dangerous chemicals or trips and slips.
The rule of ‘reasonable practicality’ states that if eliminating the hazard makes it impossible for the construction service to be delivered then the risks associated with the hazard should be eliminated. An example of this would be wearing a safety harnesses and having a supervisor while working at heights (see level 2).
Level 2 of risk management strategies
If eliminating a hazard or all of the risks associated with it is not reasonably practicable then there are several other approaches that can minimise the involved risks. These risk management tools and techniques include:
- The use of risk assessment engineering controls (eg warning signage, noise barriers, maintenance of machinery)
- Substituting the hazard with a safer alternative
- Isolating the hazard from workers and other affected persons
Level 3 of risk management strategies
This is the least effective and least reliable risk management system because it relies on human behaviour and supervision. When used in isolation, level three of the risk management framework should be carried out in line with appropriate administrative controls (eg rest breaks, job rotations) and with the use of personal protective equipment (PPE).
In regards to the proper use of PPE, regulation 44-47 of the Work Health and Safety Codes of Practice state that the equipment must be:
- “selected to minimise the risk to health and safety”
- “suitable for the nature of the work and any hazard associated with the work”
- “maintained, repaired or replaced so it continues to minimise the risk”
- “a suitable size and fit and [be] reasonably comfortable for the person wearing it”
- “used and worn by the worker, so far is reasonably practicable”
- worn “…in accordance with any information, training or reasonable instruction.”
It is recommended that level 3 risk management strategies be used in conjunction with methods from level 2 or 1 where possible.
For more information on occupational health and safety regulations or on the risk assessment process, check out the SafeWorkPro Blog.