Safe Work Australia
In the past, Australia’s vast array of workplace regulations made OHS compliance about as easy as blindfolded origami. Regulatory standards changed from state to state and figuring out which worksafe Australia codes of practice applied to which job required scrolling through pages of health and safety laws written in complicated legal-lingo. This cost businesses time and money, so in 2008 Safe Work Australia was established with the aim of streamlining this process.
Understanding the role of Safe Work Australia is central to comprehending the broader network of OHS regulations. Although the Work Health and Safety Act is long and complicated, Safe Work Australia works to standardise health and safety laws, prepare workplace codes of practice and suggest policy improvements to the government. In essence, Safe Work Australia is a model of health and safety codes of practice and OHS laws and regulations, that is reviewed by the government and then adopted by the respective states and territories.
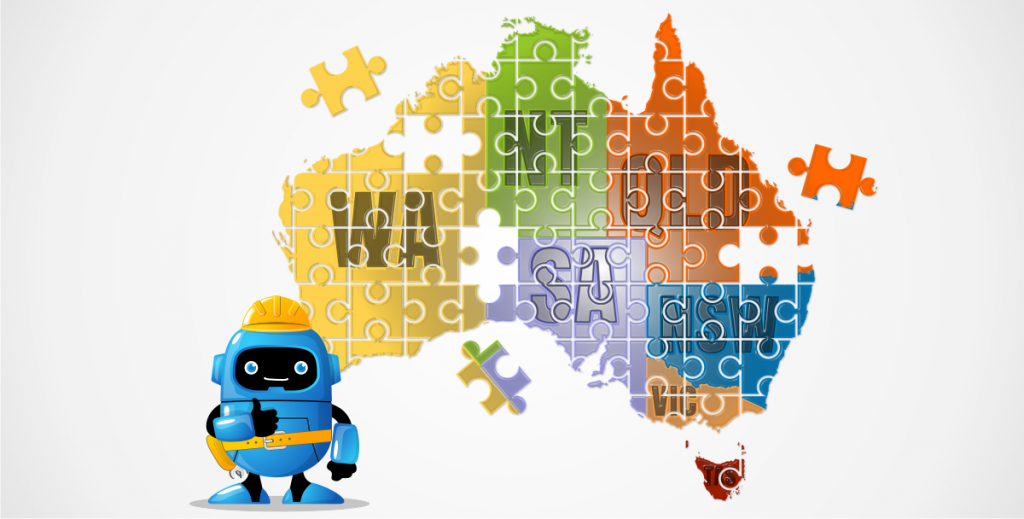
Safe Work Australia Council
Safe Work Australia council is comprised of an independent chairperson, representatives of the federal government and from each state or territory, representatives from workers groups like the Australia Council of Trade Unions, representatives of employer groups and a Chief Executive Officer. As a statutory agency independent of partisan politics, Safe Work Australia aims to develop and maintain workplace safety policy that serves the interests of all parties in a fair and balanced manner.
But what is the role of Safe Work Australia? Well its key functions as set out in the Safe Work Australia Act are to:
• Develop a national occupational health and safety policy and workplace compensation
• Prepare a model OHS Act, work health and safety codes of practice and regulations
• Review and revise laws, the workplace health and safety codes of practice and regulations if necessary
• Develop a nationally consistent policy for the compliance and enforcement of workplace health and safety legislation
• Monitor the adoption process by the Commonwealth, states and territories of health and safety legislations, codes of practice, regulations and compliance and enforcement policy
• Collect, analyse and publish any data or research relating to OHS policies and procedures, and Australian workers compensation in order to better inform the policy development process
• Raise awareness of OHS and workers’ compensation issues
It should be noted though that Safe Work Australia is not the department of workplace health and safety so its proposals don’t become law until the government signs off on any changes. This approval process happens on two levels. Firstly the Workplace Relations Ministers Council (WRMC) oversees Safe Work Australia and directs their strategic and operation direction. The WRMC is made up of the state and territory leaders responsible for industrial safety topics, workplace relations and workers’ compensation matters. So it’s mostly ministers from the related portfolios like industrial relations. When the WRMC is happy with what Safe Work Australia is proposing they collectively sign off on the agreement and the proposal then becomes a Bill to be put to the respective state’s or territory’s parliament. If the Bill is passed, then you’ve got a new set of laws and regulations sanctioned by the government and enshrined by Safe Work Australia.
It seems like a long-winded process but the eventual goal of Safe Work Australia is to standardise all the OHS safety regulations, laws and codes of practice into one consistent national policy. When achieved this will mean that the rules of workplace health and safety Queensland will be exactly the same as those in NSW or any other state or territory. With everyone on the same OHS page it will make it easier for businesses to conduct their work across state lines and grow.